
{Tea top row: cellulose fibres - viscose jersey, cotton muslin, cotton plain weave}
{Bottom row l-r: Silk pongee, wool fibres, cellulose fibres}
The basics
First drink lots of tea! Save the leaves or tea bags (I freeze mine in a ziplock bag) until you have enough. You'll need about the same weight of tea as fibre.
Always use rubber gloves for dyeing, and never use utensils afterwards for food.
Boil up the tea in water for about an hour. Use a stainless steel or enamel pan that's only used for dyeing.
Meanwhile wash your fibre to remove any dressings/grease. I use a special detergent called synthrapol but you can also use washing up liquid. For wool and other protein fibre handwash gently. For cotton and other cellulose fabric you can use a washing machine (fibre/yarn is probably best handwashed too). Leave your fibre wet.
Remove the tea bags/leaves from the dye bath (either strain it or fish out the bags).
If you're using wool any big change in temperature can make it felt, so either cool the dyebath down, or slowly wash the wool in warmer and warmer water.
Immerse your fibre in the dyebath and very slowly bring the lot to a boil (or a gentle simmer for silk). Stir regularly and gently until it's been boiling for around an hour, then turn off the heat and let it soak until cooled (keep stirring though).
Wash your fibre with detergent until the water runs clear, then dry out of direct sunlight.
You can re-use your dyebath a good few times, each time the colour will be lighter.

{Tea + Iron L-R: Silk pongee, wool fibres, wool fibres, cellulose fibres}
Mordants
Tea is a substantive dye so it doesn't need a mordant to help the colour hold fast. Different mordants will change the colour though. Alum mordant is great for wool and silk . For cotton etc. I've tried combinations of alum and tannin with soda ash. These are all done before the fibre is dyed.
You can also add iron to the dyebath for the last 15 minutes. Iron darkens (saddens) the colours, yay!
I've chosen these mordants as they're the safest to use; but always wear rubber gloves, and a mask when handling powders.
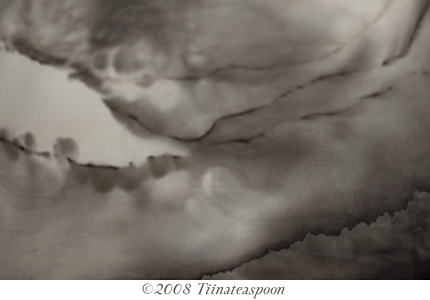
More experiments...
Rust dyeing can be combined with tea dye. These cotton plain weave samples were rusted with iron wire for a week, then overdyed with tea.
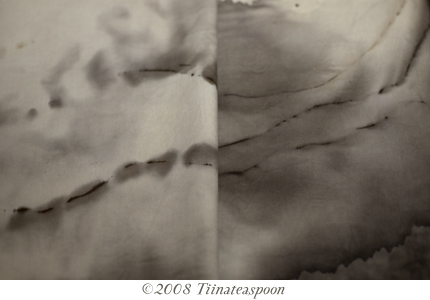
For more information and natural dye supplies...
Websites:
naturaldyes.org
aurora silk
earthues
dharma trading
fibrecrafts
Books:
(I've only included books which I own and have read.)
Natural dyes - Linda Rudkin (ISBN 978-0-7136-7955-7)
A great book which covers lots of aspects of natural dyeing, with plenty of sample pictures too! If I could only have one book on natural dyes this would be it.
The dyer's companion - Dagmar Klos (ISBN 1-931499-51-9)
A fantastic basic textbook covering natural and synthetic dyes.
A dyer's manual - Jill Goodwin (ISBN 0-9544401-0-2)
Doesn't have many sample colour pictures, but includes a long list of plants, the parts used, and the colours they may yield.
The craft of natural dyeing - Jenny Dean (ISBN 085532744-8)
A lovely book with good pictures. Not a must-have though, but a nice addition.
A dyer's garden - Rita Buchanan (ISBN 1-883010-07-1)
Useful if you're planning to grow your own dye plants, including which ones not to grow!
Dye plants and dyeing - John and Margaret Cannon (ISBN 1-871569-74-5)
Beautifully illustrated with botanical drawings. Great background reading for the biology of plant dyes.
Natural dyes, fast or fugitive - Gill Dalby (ISBN 0-9525274-0-5)
A scientific look at light and wash fastness of natural dyes, with recipes and information on how to test your dyed fibres at home.
Rust and Clay dyeing - Kimberly Baxter Packwood
A lovely book for those wishing to experiment with rust, and from a great Etsy seller too!